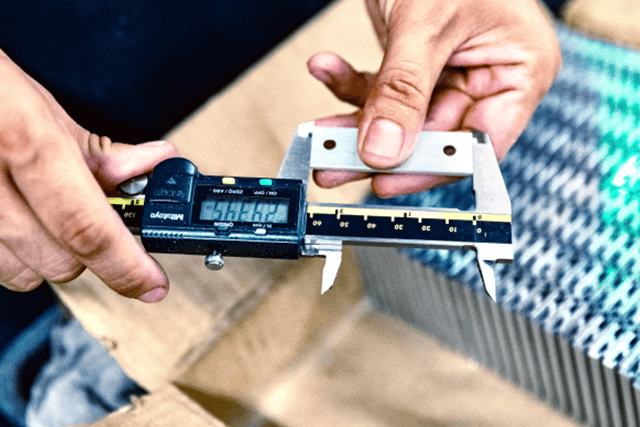
Challenges and Considerations in Designing Custom Aluminum Extrusions
25 October 2024Designing custom aluminum extrusions presents both exciting opportunities and technical challenges. Engineers and designers must consider multiple factors to create effective and efficient profiles that meet the exacting standards of diverse applications. The versatility of aluminum, along with its strength, recyclability, and adaptability, makes it an ideal material for various industries. However, the design process requires careful planning from conceptualization to finishing, with several key steps and challenges that must be addressed to achieve a successful outcome.
The Basics of Custom Aluminum Extrusion Design
Custom aluminum extrusion design focuses on creating unique aluminum profiles to suit specific requirements. Unlike standard extrusions, custom designs allow for more precise dimensions and tailored functionalities, ensuring that the extruded part fulfills its intended purpose.
The process begins with selecting the appropriate aluminum alloy, which is critical for achieving desired properties like strength, corrosion resistance, or conductivity. For example, 6061 and 6063 alloys are commonly used due to their excellent mechanical properties and workability.
Once the alloy is chosen, designers develop a profile that takes full advantage of aluminum’s ability to be extruded into complex shapes. Extrusion allows for near-net-shape manufacturing, which can reduce waste, minimize secondary machining, and lower costs. Moreover, extrusions can be designed with multiple voids, intricate cross-sections, and precise tolerances, making them ideal for structural applications.
What Steps Does Custom Aluminum Extrusion Design Entail?
The custom extrusion design process is structured around several key stages, each vital to guaranteeing the final product meets performance and aesthetic expectations.
Conceptual and Detailed Design
Designers first focus on the overall functionality of the extrusion. This stage requires a thorough understanding of how the part will be used, including what loads it will bear, how it interacts with other components and any environmental factors it might face. Tools such as 3D modeling software and Finite Element Analysis (FEA) are typically employed to simulate the behavior of the design under real-world conditions. FEA allows for optimization of the extrusion’s weight, strength, and material usage, avoiding unnecessary design complexities.
Simulation and Testing
Before creating the extrusion die, simulations are run to predict how the material will flow during the extrusion process. These simulations help identify potential weak points in the profile and make sure that the die will produce the desired results. Testing may also involve stress and thermal analysis to evaluate how the part will perform under various loads or in different environments.
Die Creation (Design and Manufacturing)
After refining the design, the extrusion die is manufactured. The die is a custom tool that shapes the aluminum as it is forced through under immense pressure. Precision in die creation is critical, as any flaws can lead to dimensional inaccuracies in the final product. This stage also involves selecting the appropriate die material, typically hardened steel, to withstand the stresses of the extrusion process.
Extrusion Process
The actual extrusion process begins with heating the aluminum billet to a temperature that allows it to flow easily through the die. The heated material is then pushed through the die using a hydraulic press. Upon exiting, the profile cools and hardens into the desired shape. This process allows for long, continuous profiles that can later be cut to the required lengths.
Fabrication, Cutting, and Machining
After extrusion, additional fabrication processes such as cutting, drilling, or CNC machining may be required to achieve the final specifications. These secondary operations enable further customization, allowing for more detailed features like holes, notches, or specific connection points.
Surface Finishing
The final step in the process is surface finishing, which enhances both the appearance and functionality of the extruded profile. Common finishes include anodizing for corrosion resistance, powder coating for durability, or polishing for a sleek aesthetic. The type of finishing selected depends on the application and environmental factors the profile will encounter.
Challenges and Considerations When Designing Custom Aluminum Extrusions
Several challenges arise during the custom extrusion design process, requiring careful attention to detail.
Choosing the Right Alloy
Aluminum alloys vary significantly in terms of strength, formability, and corrosion resistance. Selecting the right alloy is crucial for ensuring that the extruded profile meets the performance requirements of its application. For instance, while 6063 is ideal for architectural applications due to its superior surface finish, 6061 is often used in structural applications for its high strength.
Choosing the Best Temper
Tempering affects the hardness and ductility of the aluminum. Designers must carefully select the appropriate temper based on the mechanical properties needed for the final product. For example, T6 tempering is often used to achieve maximum strength, while other tempers may be chosen for improved formability.
Design Complexities
Profiles with intricate cross-sections or tight tolerances present additional challenges. Complex shapes may require more advanced die designs and higher-quality control during the extrusion process to prevent defects such as warping or surface imperfections. Dimensional tolerances must be well defined, especially if the extrusion will be part of a larger assembly where precision is critical.
Surface Finishing Options
The finish applied to the extrusion can significantly impact its durability and appearance. For parts exposed to the elements, anodizing is often chosen for its ability to enhance corrosion resistance while offering an aesthetically pleasing surface. However, not all surface finishes are compatible with every alloy or temper, so these factors must be considered early in the design process.
Custom Fabrications
Further machining or custom fabrications may be necessary depending on the complexity of the design. Processes like cutting, drilling, and notching can add to the cost and time required to complete the extrusion, but they are often essential to meeting detailed design specifications.
Cost Considerations
While aluminum extrusion is generally more cost-effective than other manufacturing methods, especially for complex shapes, it’s important to balance the cost of custom dies, alloy selection, and additional machining with the project’s overall budget. Advanced simulations and thorough planning can help minimize unexpected costs later in the production process.
Finding the Right Partner for Custom Extrusion Design
Choosing the right partner for custom aluminum extrusion is key to overcoming these challenges and achieving a successful outcome. With decades of experience in producing complex, high-quality extrusions, Paramount Extrusions offers the expertise needed to guide projects from concept to completion. Whether it’s selecting the best alloy, designing intricate cross-sections, or applying the perfect finish, Paramount’s team is equipped to handle custom orders of any scale. Contact Paramount Extrusions today to discuss your next project and experience the advantages of working with a trusted industry leader.