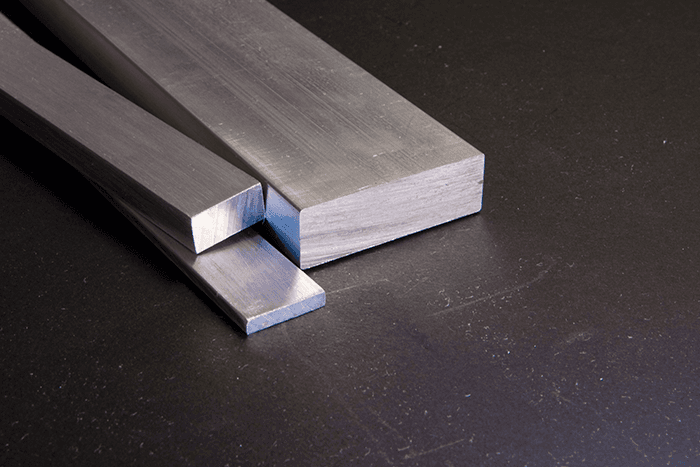
Paramount’s Guide to the Best Type of Aluminum Tempering
12 September 2024Aluminum is one of the most versatile metals available, prized for its lightweight, corrosion-resistant, and recyclable properties. However, to unlock its full potential – especially in demanding applications – aluminum often requires controlled heating and cooling in order to produce a desired end result. This process, known as aluminum tempering, significantly enhances the metal’s mechanical properties, making it suitable for a wide range of industrial uses. In this guide, we’ll explore the various types of aluminum tempering, their benefits, and how Paramount Extrusions’ expertise can help you choose the right solution for your specific needs.
What is Aluminum Tempering?
Aluminum tempering is an intricate treatment process designed to increase the strength, hardness, and durability of aluminum alloys. This is achieved by heating the aluminum to a specific temperature, then cooling it in a controlled manner. By altering the metal’s microstructure, tempering significantly improves its mechanical properties, making it more suitable for high-performance applications.
Tempering differs from other heat treatment methods, such as annealing or quenching, in that it is specifically focused on enhancing the material’s strength and resilience without compromising its workability. While annealing softens aluminum for easier forming, and quenching rapidly cools it to lock in certain properties, aluminum tempering carefully balances heat and cooling to deliver a durable and versatile final product.
The importance of aluminum tempering cannot be overstated. Industries ranging from aerospace to automotive rely on this process to produce components that can withstand extreme conditions. Whether it’s the frame of an airplane or the body of a high-performance vehicle, aluminum tempering ensures that the metal performs reliably under stress, making it an essential process for any application where strength and longevity are critical.
What Are the Different Types of Aluminum Tempering?
There are several tempering processes used to treat aluminum, each resulting in different mechanical properties and suitable for specific applications. Understanding the differences between these processes is crucial for selecting the right type of aluminum tempering for your project.
- T1 Tempering: T1 tempering involves cooling the aluminum after it is shaped by a hot working process, such as extrusion, and then naturally aging it at room temperature. This tempering process results in a lower strength alloy compared to T5 or T6, but it maintains a good level of workability and is often used in applications where rapid strength is not a primary requirement. T1 is commonly used for components that need minimal machining or forming after extrusion, such as automotive trim, structural beams, and basic architectural shapes.
- T6 Tempering: Perhaps the most widely recognized, T6 tempering involves solution heat treatment followed by artificial aging. This process results in a high-strength alloy, ideal for structural components in the aerospace and automotive industries, where both strength and weight are key considerations.
- T5 Tempering: This process involves cooling the aluminum after extrusion and then artificially aging it to achieve increased hardness. T5 tempering is often used in the construction industry, particularly in window frames, door frames, and other architectural elements where enhanced strength and durability are required.
- T4 Tempering: Unlike T6 and T5, T4 tempering involves a natural aging process after solution heat treatment. This type is typically used in automotive body panels, where a balance between formability and strength is necessary. The material is softer than T6 but can be further aged (to T6 levels) to reach full hardness if needed.
- T52 Tempering: T52 tempering is a special heat treatment process involving artificial aging, similar to T5 but optimized to reduce residual stresses in the aluminum. This results in a temper with slightly less hardness but improved ductility and toughness, making it less prone to cracking during forming or welding. T52 is often used in applications requiring enhanced resistance to cracking or when the aluminum component is subject to further forming processes, such as bending or complex machining.
Each of these tempering processes provides specific advantages, depending on the intended application. By understanding these distinctions, manufacturers can select the most appropriate aluminum tempering method to guarantee that their products meet industry standards and perform as expected in their respective environments.
Benefits and Applications of Aluminum Tempering
Aluminum tempering offers more than just increased strength; it enhances wear, fatigue, and corrosion resistance, making it ideal for industries requiring durable and reliable materials:
- Strength and Durability: Tempered aluminum is significantly stronger than untreated aluminum, making it essential for components that must bear heavy loads or withstand impact. This strength makes it a top choice for structural applications in construction and transportation.
- Corrosion Resistance: The tempering process enhances aluminum’s corrosion resistance, particularly in harsh environments. This is crucial for applications like marine structures, outdoor architecture, and automotive parts, where exposure to moisture and chemicals is a concern.
- Versatility: Tempered aluminum is used across various industries due to its adaptability and performance. In aerospace, it’s vital for aircraft frames, wings, and fuselage components. In the automotive sector, it’s found in engine blocks, wheels, and body panels.
- Workability: Electronics industries utilize tempered aluminum for heat sinks and enclosures because of its excellent thermal conductivity and lightweight properties. Softer aluminum tempers, like T1 or T4, are particularly beneficial in assembly and installation processes, as they can be easily formed, bent, or manipulated to fit precise radii with simple hand tools. This makes them ideal for applications where quick adjustments or on-site modifications are necessary.
Partnering with Paramount’s Aluminum Tempering Capabilities
When it comes to aluminum tempering, expertise matters. Paramount Extrusions brings decades of experience and state-of-the-art technology to every project, certifying that each piece of tempered aluminum meets the highest industry standards. Whether you’re in aerospace, automotive, construction, or electronics, our tailored tempering solutions are designed to deliver unparalleled performance and reliability.
Paramount has successfully completed projects across various industries, consistently providing clients with high-quality, tempered aluminum products that stand up to the most demanding applications. Our advanced techniques and commitment to quality make us the ideal partner for your next aluminum tempering project.
Ready to enhance your products with superior aluminum tempering? Contact Paramount Extrusions today to start your project, and experience the difference that our depth of expertise and innovation can make.